Filtering by
- Creators: Arizona Board of Regents
- Creators: Hsu, Keng H.
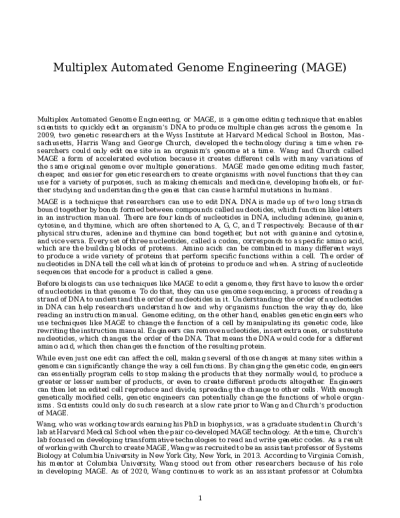
Multiplex Automated Genome Engineering, or MAGE, is a genome editing technique that enables scientists to quickly edit an organism’s DNA to produce multiple changes across the genome. In 2009, two genetic researchers at the Wyss Institute at Harvard Medical School in Boston, Massachusetts, Harris Wang and George Church, developed the technology during a time when researchers could only edit one site in an organism’s genome at a time. Wang and Church called MAGE a form of accelerated evolution because it creates different cells with many variations of the same original genome over multiple generations. MAGE made genome editing much faster, cheaper, and easier for genetic researchers to create organisms with novel functions that they can use for a variety of purposes, such as making chemicals and medicine, developing biofuels, or further studying and understanding the genes that can cause harmful mutations in humans.

In-process laser heating technique delivers a cost-efficient way to improve mechanical and geometrical properties to nearly isotropic and extremely smooth, respectively. The technique involves the incorperation of a solid-state laser into a commercial off-the-shelf 3D printer, mechanical system to allow controllable laser allumination on desired surfaces, and a gcode postprocesser to proper control of the mechanical system. This process uses laser for local heating, to enhance mass transfer between boundaries or to enhance surface reflow to smooth surface irregularity, to improve mechanical and geometrical properties. Only less than 3 W of laser power (CO2 laser) was used for high temperature material like PEEK and Ultem; less than 1 W (808nm laser) was found to be sufficient for achieving optimal properties for PLA. This technique has the potential for after-market integration into most commercial FFF 3D printers to achieved nearly isotropic and smooth 3D printed objects with various thermoplastic polymers.