Theses and Dissertations
Displaying 1 - 5 of 5
Filtering by
- All Subjects: manufacturing
- Creators: Department of Supply Chain Management

Description
Upon investigating the current state of the high scrap problem at Niagara Bottling's Phoenix manufacturing facility, it was found that 49% of the scrap was being generated at the bottling lines in the form of plastic bottles, and 39% of scrap took the form of preforms accumulated at either the bottling lines or the injection molding machines. The scope of this project includes all forms of polyethylene terephthalate (PET), but the large accumulation of scrap in these areas suggests a primary focus on the bottling lines and the injection molding machines. Further analysis of the bottling lines found that the filler at each line as well as the blower on line X1 were the biggest contributors to the scrap accumulation problem. Each of these machines was seeing over 0.4% of bottles rejected at the visual inspection units. Due to the underlying status and quality issues of the injection molding machines that were beyond the scope of this project, this process was only investigated for solutions involving the overall processes and people. Based on the data and process flow analysis there were several solutions proposed including a root-cause analysis of the highest faulting machines, the repair of the injection molding overhead conveyor systems, the creation of a low waste environment, and the implementation a scrap tracking and analysis process. Based on the current high variability in the scrap experience across all machines, it is recommended that Niagara Phoenix pursue the scrap tracking and analysis alternative. After the implementing the scrap tracking and analysis process, the initial results were encouraging and could potentially warrant the investment in a software platform that could automate the collection of data necessary for this process. Based on the initial results of the manual collection and analysis process, each individual line show signs of potential reduction in the scrap rate of over 50%. According to this improvement, purchasing the software platform would see a payoff period of only 36 days.
ContributorsSanchez, Thomas Camden (Author) / Kellso, James (Thesis director) / Lupe, Munoz (Committee member) / Barrett, The Honors College (Contributor) / School of International Letters and Cultures (Contributor) / Department of Supply Chain Management (Contributor)
Created2015-05

Description
Over the course of six months, we have worked in partnership with Arizona State University and a leading producer of semiconductor chips in the United States market (referred to as the "Company"), lending our skills in finance, statistics, model building, and external insight. We attempt to design models that help predict how much time it takes to implement a cost-saving project. These projects had previously been considered only on the merit of cost savings, but with an added dimension of time, we hope to forecast time according to a number of variables. With such a forecast, we can then apply it to an expense project prioritization model which relates time and cost savings together, compares many different projects simultaneously, and returns a series of present value calculations over different ranges of time. The goal is twofold: assist with an accurate prediction of a project's time to implementation, and provide a basis to compare different projects based on their present values, ultimately helping to reduce the Company's manufacturing costs and improve gross margins. We believe this approach, and the research found toward this goal, is most valuable for the Company. Two coaches from the Company have provided assistance and clarified our questions when necessary throughout our research. In this paper, we begin by defining the problem, setting an objective, and establishing a checklist to monitor our progress. Next, our attention shifts to the data: making observations, trimming the dataset, framing and scoping the variables to be used for the analysis portion of the paper. Before creating a hypothesis, we perform a preliminary statistical analysis of certain individual variables to enrich our variable selection process. After the hypothesis, we run multiple linear regressions with project duration as the dependent variable. After regression analysis and a test for robustness, we shift our focus to an intuitive model based on rules of thumb. We relate these models to an expense project prioritization tool developed using Microsoft Excel software. Our deliverables to the Company come in the form of (1) a rules of thumb intuitive model and (2) an expense project prioritization tool.
ContributorsAl-Assi, Hashim (Co-author) / Chiang, Robert (Co-author) / Liu, Andrew (Co-author) / Ludwick, David (Co-author) / Simonson, Mark (Thesis director) / Hertzel, Michael (Committee member) / Barrett, The Honors College (Contributor) / Department of Information Systems (Contributor) / Department of Finance (Contributor) / Department of Economics (Contributor) / Department of Supply Chain Management (Contributor) / School of Accountancy (Contributor) / School of Mathematical and Statistical Sciences (Contributor) / Mechanical and Aerospace Engineering Program (Contributor) / WPC Graduate Programs (Contributor)
Created2015-05

Description
The purpose of this creative project was to investigate the process a start-up or small business must complete to have a sell-able apparel product manufactured. The initial goal of the project was to experience the manufacturing process from start to finish and complete a full production run from a professional manufacturer. The conclusion found was that start-ups and small businesses will have to begin production within the United States.
ContributorsBour, Melissa (Author) / Sewell, Dennita (Thesis director) / Rogers, Dale (Committee member) / Ellis, Naomi (Committee member) / Dean, Herberger Institute for Design and the Arts (Contributor) / Department of Supply Chain Management (Contributor) / Dean, W.P. Carey School of Business (Contributor) / Barrett, The Honors College (Contributor)
Created2019-05

Description
Single-use plastic has rapidly increased pollution in the United States, and the urgency to address its growing consequences is a complex undertaking. Significantly contributing to plastic pollution is the waste of single-use beverage plastics like cups and straws. In order to make impactful changes in the supply chain of single-use beverage plastics, we must first understand the stakeholders involved and the current extent of their actions. Therefore, this paper will investigate how stakeholders elicit sustainable changes to improve supply chain practices in this particular situation. We will use principles of sustainable supply chain management including corporate social responsibility and the triple bottom line model as the theoretical framework. Methodology consists of a stakeholder analysis where we conduct literature review, a consumer survey analysis, and interviews with industry experts to examine how various stakeholders elicit sustainably focused change. Essential insights made will be to understand different stakeholder actions and perspectives in relation to single-use beverage plastics, and how they contribute to creating sustainable changes in the larger context of plastic pollution control.
ContributorsGalaviz, Christopher (Author) / Wiedmer, Robert (Thesis director) / Oke, Adegoke (Committee member) / Department of Supply Chain Management (Contributor) / Dean, W.P. Carey School of Business (Contributor) / Barrett, The Honors College (Contributor)
Created2019-05
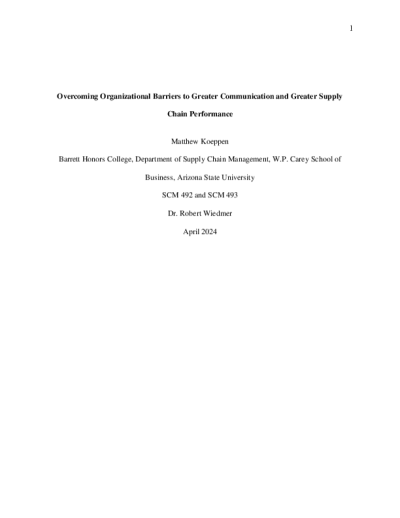
Description
This research examines supply chain performance and antecedents to better supply chain performance in manufacturing organizations, with a focus on manufacturing organizations following engineer-to-order and assemble-to-order production models. The variables of supply chain integration, internal communication, employee satisfaction, leader support, and the alignment of information and communication technology are empirically supported in affecting supply chain performance, and thus carry managerial and organizational implications in how they can be influenced, ideally for the benefit of manufacturing organizations. The data gathered for this study was obtained through interviews with sourcing professionals, as well as surveys distributed to corporate manufacturing employees. The findings on these variables fall in line with previous research explored in the report, adding credibility to previous studies, as well as their associated recommendations and implications. Organizational management and leadership, to improve supply chain performance, must strategically integrate information and communication technology, be clear and consistent in their messaging to employees, engage in effective conflict resolution, and provide support for necessary transparency and communication-enhancing initiatives.
ContributorsKoeppen, Matthew (Author) / Wiedmer, Robert (Thesis director) / Hogan, Michael (Committee member) / Barrett, The Honors College (Contributor) / Department of Management and Entrepreneurship (Contributor) / Department of Supply Chain Management (Contributor)
Created2024-05