Matching Items (3)

Description
A hybrid molecular dynamics (MD) simulation framework is developed to emulate mechanochemical reaction of mechanophores in epoxy-based nanocomposites. Two different force fields, a classical force field and a bond order based force field are hybridized to mimic the experimental processes from specimen preparation to mechanical loading test. Ultra-violet photodimerization for mechanophore synthesis and epoxy curing for thermoset polymer generation are successfully simulated by developing a numerical covalent bond generation method using the classical force field within the framework. Mechanical loading tests to activate mechanophores are also virtually conducted by deforming the volume of a simulation unit cell. The unit cell deformation leads to covalent bond elongation and subsequent bond breakage, which is captured using the bond order based force field. The outcome of the virtual loading test is used for local work analysis, which enables a quantitative study of mechanophore activation. Through the local work analysis, the onset and evolution of mechanophore activation indicating damage initiation and propagation are estimated; ultimately, the mechanophore sensitivity to external stress is evaluated. The virtual loading tests also provide accurate estimations of mechanical properties such as elastic, shear, bulk modulus, yield strain/strength, and Poisson’s ratio of the system. Experimental studies are performed in conjunction with the simulation work to validate the hybrid MD simulation framework. Less than 2% error in estimations of glass transition temperature (Tg) is observed with experimentally measured Tgs by use of differential scanning calorimetry. Virtual loading tests successfully reproduce the stress-strain curve capturing the effect of mechanophore inclusion on mechanical properties of epoxy polymer; comparable changes in Young’s modulus and yield strength are observed in experiments and simulations. Early damage signal detection, which is identified in experiments by observing increased intensity before the yield strain, is captured in simulations by showing that the critical strain representing the onset of the mechanophore activation occurs before the estimated yield strain. It is anticipated that the experimentally validated hybrid MD framework presented in this dissertation will provide a low-cost alternative to additional experiments that are required for optimizing material design parameters to improve damage sensing capability and mechanical properties.
In addition to the study of mechanochemical reaction analysis, an atomistic model of interphase in carbon fiber reinforced composites is developed. Physical entanglement between semi-crystalline carbon fiber surface and polymer matrix is captured by introducing voids in multiple graphene layers, which allow polymer matrix to intertwine with graphene layers. The hybrid MD framework is used with some modifications to estimate interphase properties that include the effect of the physical entanglement. The results are compared with existing carbon fiber surface models that assume that carbon fiber has a crystalline structure and hence are unable to capture the physical entanglement. Results indicate that the current model shows larger stress gradients across the material interphase. These large stress gradients increase the viscoplasticity and damage effects at the interphase. The results are important for improved prediction of the nonlinear response and damage evolution in composite materials.
In addition to the study of mechanochemical reaction analysis, an atomistic model of interphase in carbon fiber reinforced composites is developed. Physical entanglement between semi-crystalline carbon fiber surface and polymer matrix is captured by introducing voids in multiple graphene layers, which allow polymer matrix to intertwine with graphene layers. The hybrid MD framework is used with some modifications to estimate interphase properties that include the effect of the physical entanglement. The results are compared with existing carbon fiber surface models that assume that carbon fiber has a crystalline structure and hence are unable to capture the physical entanglement. Results indicate that the current model shows larger stress gradients across the material interphase. These large stress gradients increase the viscoplasticity and damage effects at the interphase. The results are important for improved prediction of the nonlinear response and damage evolution in composite materials.
ContributorsKoo, Bonsung (Author) / Chattopadhyay, Aditi (Thesis advisor) / Dai, Lenore (Committee member) / Jiang, Hanqing (Committee member) / Jiao, Yang (Committee member) / Rajadas, John (Committee member) / Arizona State University (Publisher)
Created2017

Description
The problem of catastrophic damage purveys in any material application, and minimizing its occurrence is paramount for general health and safety. We have successfully synthesized, characterized, and applied dimeric 9-anthracene carboxylic acid (Di-AC)-based mechanophores particles to form stress sensing epoxy matrix composites. As Di-AC had never been previously applied as a mechanophore and thermosets are rarely studied in mechanochemistry, this created an alternative avenue for study in the field. Under an applied stress, the cyclooctane-rings in the Di-AC particles reverted back to their fluorescent anthracene form, which linearly enhanced the overall fluorescence of the composite in response to the applied strain. The fluorescent signal further allowed for stress sensing in the elastic region of the stress\u2014strain curve, which is considered to be a form of damage precursor detection. Overall, the incorporation of Di-AC to the epoxy matrix added much desired stress sensing and damage precursor detection capabilities with good retention of the material properties.
ContributorsWickham, Jason Alexander (Co-author) / Nofen, Elizabeth (Co-author, Committee member) / Koo, Bonsung (Co-author) / Chattopadhyay, Aditi (Co-author) / Dai, Lenore (Co-author, Thesis director) / Chemical Engineering Program (Contributor) / Barrett, The Honors College (Contributor)
Created2016-05
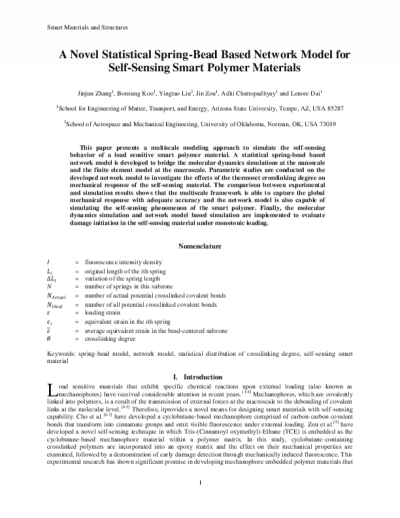
Description
This paper presents a multiscale modeling approach to simulating the self-sensing behavior of a load sensitive smart polymer material. A statistical spring-bead based network model is developed to bridge the molecular dynamics simulations at the nanoscale and the finite element model at the macroscale. Parametric studies are conducted on the developed network model to investigate the effects of the thermoset crosslinking degree on the mechanical response of the self-sensing material. A comparison between experimental and simulation results shows that the multiscale framework is able to capture the global mechanical response with adequate accuracy and the network model is also capable of simulating the self-sensing phenomenon of the smart polymer. Finally, the molecular dynamics simulation and network model based simulation are implemented to evaluate damage initiation in the self-sensing material under monotonic loading.
ContributorsZhang, Jinjun (Author) / Koo, Bonsung (Author) / Liu, Yingtao (Author) / Zou, Jin (Author) / Chattopadhyay, Aditi (Author) / Dai, Lenore (Author) / Ira A. Fulton Schools of Engineering (Contributor) / School for the Engineering of Matter, Transport and Energy (Contributor)
Created2015-08-01