Matching Items (1,574)
Filtering by
- Creators: Marine Biological Laboratory Archives

Description
In this thesis, Inception V3, a convolutional neural network model from Google, was partially retrained to categorize pipeline images based on their damage modes. The images for different damage modes of the pipeline were simulated through MATLAB to represent image data collected from in-line pipe inspection. The final convolutional layer of the model was retrained with the simulated pipeline images using TensorFlow as the base platform. First, a small-scale retraining was done with real images and simulated images to compare the differences in performance. Then, using simulated images, a 2^5 full factorial design of experiment and individual parametric studies were performed on five different chosen parameters, including training steps, learning rate, batch size, training data size and image noise. The effect of each parameter on the performance of the model was evaluated and analyzed. It is crucial to understand that due to the nature of the experiment, the learnings may or may not apply to neural network models trained for other tasks. After analyzing the results, the effects and trade-offs for each parameter are discussed in detail. In addition, a method of predicting the training time was proposed. Based on the findings, an optimized model was proposed for this training exercise, with 1180 training steps, a learning rate of 0.01, a batch size of 100 and a training data set of 200 images. The optimized model reached 87.2% accuracy with a training time of 2 minutes and 6 seconds. This study will enhance our understanding in applying machine learning techniques in damage and risk identification.
ContributorsShen, Guangqing (Author) / Liu, Yongming (Thesis director) / Ren, Yi (Committee member) / Mechanical and Aerospace Engineering Program (Contributor) / Barrett, The Honors College (Contributor)
Created2018-05

Description
Widespread knowledge of fracture mechanics is mostly based on previous models that generalize crack growth in materials over several loading cycles. The objective of this project is to characterize crack growth that occurs in titanium alloys, specifically Grade 5 Ti-6Al-4V, at the sub-cycle scale, or within a single loading cycle. Using scanning electron microscopy (SEM), imaging analysis is performed to observe crack behavior at ten loading steps throughout the loading and unloading paths. Analysis involves measuring the incremental crack growth and crack tip opening displacement (CTOD) of specimens at loading ratios of 0.1, 0.3, and 0.5. This report defines the relationship between crack growth and the stress intensity factor, K, of the specimens, as well as the relationship between the R-ratio and stress opening level. The crack closure phenomena and effect of microcracks are discussed as they influence the crack growth behavior. This method has previously been used to characterize crack growth in Al 7075-T6. The results for Ti-6Al-4V are compared to these previous findings in order to strengthen conclusions about crack growth behavior.
ContributorsNazareno, Alyssa Noelle (Author) / Liu, Yongming (Thesis director) / Jiao, Yang (Committee member) / Mechanical and Aerospace Engineering Program (Contributor) / Barrett, The Honors College (Contributor)
Created2018-05

Description
This research examines the current challenges of using Lamb wave interrogation methods to localize fatigue crack damage in a complex metallic structural component subjected to unknown temperatures. The goal of this work is to improve damage localization results for a structural component interrogated at an unknown temperature, by developing a probabilistic and reference-free framework for estimating Lamb wave velocities and the damage location. The methodology for damage localization at unknown temperatures includes the following key elements: i) a model that can describe the change in Lamb wave velocities with temperature; ii) the extension of an advanced time-frequency based signal processing technique for enhanced time-of-flight feature extraction from a dispersive signal; iii) the development of a Bayesian damage localization framework incorporating data association and sensor fusion. The technique requires no additional transducers to be installed on a structure, and allows for the estimation of both the temperature and the wave velocity in the component. Additionally, the framework of the algorithm allows it to function completely in an unsupervised manner by probabilistically accounting for all measurement origin uncertainty. The novel algorithm was experimentally validated using an aluminum lug joint with a growing fatigue crack. The lug joint was interrogated using piezoelectric transducers at multiple fatigue crack lengths, and at temperatures between 20°C and 80°C. The results showed that the algorithm could accurately predict the temperature and wave speed of the lug joint. The localization results for the fatigue damage were found to correlate well with the true locations at long crack lengths, but loss of accuracy was observed in localizing small cracks due to time-of-flight measurement errors. To validate the algorithm across a wider range of temperatures the electromechanically coupled LISA/SIM model was used to simulate the effects of temperatures. The numerical results showed that this approach would be capable of experimentally estimating the temperature and velocity in the lug joint for temperatures from -60°C to 150°C. The velocity estimation algorithm was found to significantly increase the accuracy of localization at temperatures above 120°C when error due to incorrect velocity selection begins to outweigh the error due to time-of-flight measurements.
ContributorsHensberry, Kevin (Author) / Chattopadhyay, Aditi (Thesis advisor) / Liu, Yongming (Committee member) / Papandreou-Suppappola, Antonia (Committee member) / Arizona State University (Publisher)
Created2013

Description
Additively Manufactured Thin-wall Inconel 718 specimens commonly find application in heat exchangers and Thermal Protection Systems (TPS) for space vehicles. The wall thicknesses in applications for these components typically range between 0.03-2.5mm. Laser Powder Bed Fusion (PBF) Fatigue standards assume thickness over 5mm and consider Hot Isostatic Pressing (HIP) as conventional heat treatment. This study aims at investigating the dependence of High Cycle Fatigue (HCF) behavior on wall thickness and Hot Isostatic Pressing (HIP) for as-built Additively Manufactured Thin Wall Inconel 718 alloys. To address this aim, high cycle fatigue tests were performed on specimens of seven different thicknesses (0.3mm,0.35mm, 0.5mm, 0.75mm, 1mm, 1.5mm, and 2mm) using a Servohydraulic FatigueTesting Machine. Only half of the specimen underwent HIP, creating data for bothHIP and No-HIP specimens. Upon analyzing the collected data, it was noticed that the specimens that underwent HIP had similar fatigue behavior to that of sheet metal specimens. In addition, it was also noticed that the presence of Porosity in No-HIP specimens makes them more sensitive to changes in stress. A clear decrease in fatigue strength with the decrease in thickness was observed for all specimens.
ContributorsSaxena, Anushree (Author) / Bhate, Dhruv (Thesis advisor) / Liu, Yongming (Committee member) / Kwon, Beomjin (Committee member) / Arizona State University (Publisher)
Created2021
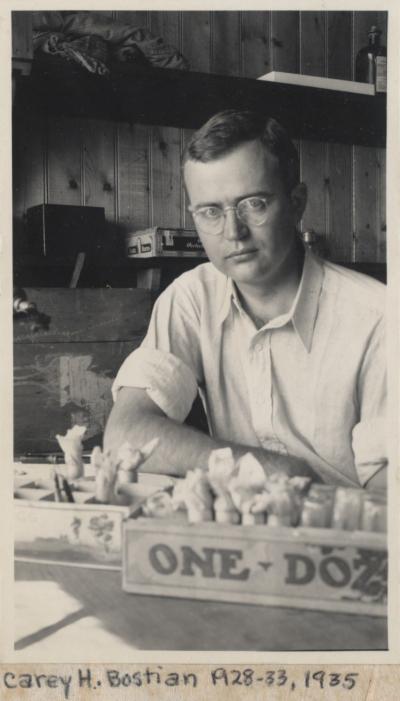
ContributorsMarine Biological Laboratory Archives (Publisher) / Arizona Board of Regents (Publisher)
Created1935
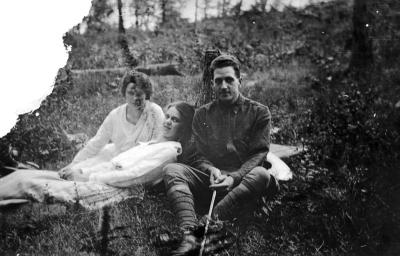
ContributorsHuettner, Alfred F. (Alfred Francis), b. 1884 (Creator) / Marine Biological Laboratory Archives (Publisher)
Created1918
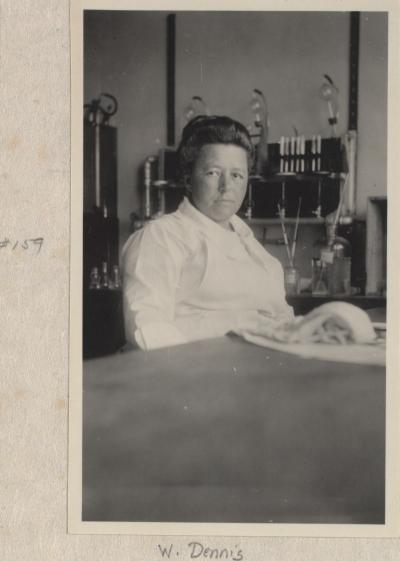
ContributorsMarine Biological Laboratory Archives (Publisher)
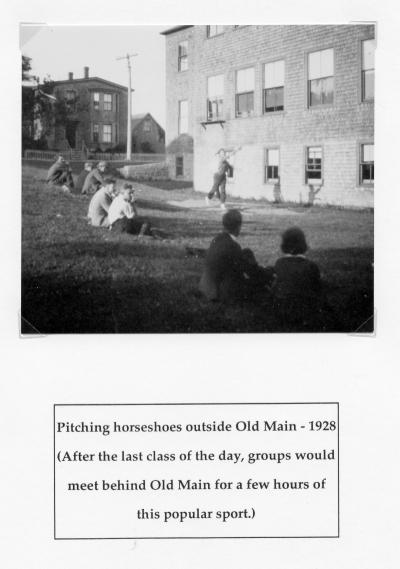
ContributorsHuettner, Alfred F. (Alfred Francis), b. 1884 (Creator) / Marine Biological Laboratory Archives (Publisher)
Created1928
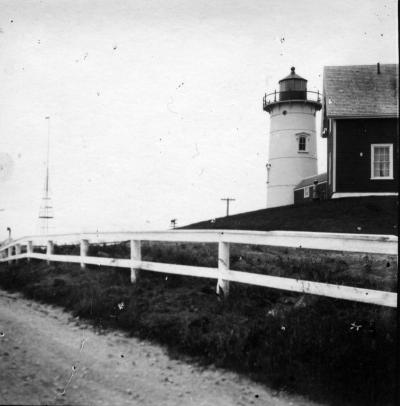
ContributorsHuettner, Alfred F. (Alfred Francis), b. 1884 (Creator) / Marine Biological Laboratory Archives (Publisher)
Created1918
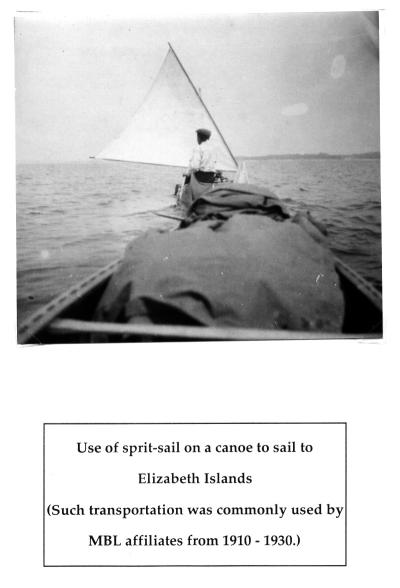
ContributorsHuettner, Alfred F. (Alfred Francis), b. 1884 (Creator) / Marine Biological Laboratory Archives (Publisher)