Matching Items (2,115)
Filtering by
- All Subjects: People

Description
Pb-free solders are used as interconnects in various levels of micro-electronic packaging. Reliability of these interconnects is very critical for the performance of the package. One of the main factors affecting the reliability of solder joints is the presence of porosity which is introduced during processing of the joints. In this thesis, the effect of such porosity on the deformation behavior and eventual failure of the joints is studied using Finite Element (FE) modeling technique. A 3D model obtained by reconstruction of x-ray tomographic image data is used as input for FE analysis to simulate shear deformation and eventual failure of the joint using ductile damage model. The modeling was done in ABAQUS (v 6.10). The FE model predictions are validated with experimental results by comparing the deformation of the pores and the crack path as predicted by the model with the experimentally observed deformation and failure pattern. To understand the influence of size, shape, and distribution of pores on the mechanical behavior of the joint four different solder joints with varying degrees of porosity are modeled using the validated FE model. The validation technique mentioned above enables comparison of the simulated and actual deformation only. A more robust way of validating the FE model would be to compare the strain distribution in the joint as predicted by the model and as observed experimentally. In this study, to enable visualization of the experimental strain for the 3D microstructure obtained from tomography, a three dimensional digital image correlation (3D DIC) code has been implemented in MATLAB (MathWorks Inc). This developed 3D DIC code can be used as another tool to verify the numerical model predictions. The capability of the developed code in measuring local displacement and strain is demonstrated by considering a test case.
ContributorsJakkali, Vaidehi (Author) / Chawla, Nikhilesh K (Thesis advisor) / Jiang, Hanqing (Committee member) / Solanki, Kiran (Committee member) / Arizona State University (Publisher)
Created2011

Description
Pb-free solder joints are commonly used as interconnects in semiconductor packaging. One of the major defects affecting the mechanical performance of solder joints are reflow pores that form during processing. These pores exhibit significant variability in size and distribution, and understanding the effects of pore geometry on failure is an important reliability concern. In this thesis, the pore microstructures of solder joint samples and the localized plastic deformation around individual pores was characterized in 3D using lab scale X-ray Microtomography. To observe the deformation of a solder joint in 3D, a solder joint was imaged with Microtomography after reflow and then deformed in shear in several loading steps with additional tomography data taken between each. The 3D tomography datasets were then segmented using the 3D Livewire technique into regions corresponding to solder and pores, and used to generate 3D models of the joint at each strain value using Mimics software. The extent of deformation of individual pores in the joint as a function of strain was quantified using sphericity measurements, and correlated with the observed cracking in the joint. In addition, the error inherent in the data acquisition and 3D modeling process was also quantified. The progression of damage observed with X-ray Microtomography was then used to validate the deformation and failure predicted by a Finite Element (FE) simulation. The FE model was based on the as-reflowed tomography data, and incorporated a ductile damage failure model to simulate fracture. Using the measured sphericity change and cracking information obtained from the tomography data, the FE model is shown to correctly capture the broad plastic deformation and strain localization seen in the actual joint, as well as the crack propagation. Lastly, Digital Image Correlation was investigated as a method of obtaining improved local strain measurements in 3D. This technique measures the displacement of the inherent microstructural features of the joint, and can give localized strain measurements that can be directly comparable to that predicted by modeling. The technique is demonstrated in 2D on Pb-Sn solder, and example 3D data is presented for future analysis.
ContributorsPadilla, Erick (Author) / Chawla, Nikhilesh (Thesis advisor) / Alford, Terry (Committee member) / Krause, Stephen (Committee member) / Arizona State University (Publisher)
Created2012

Description
The study of deflagration to detonation transition (DDT) in explosives is of prime importance with regards to insensitive munitions (IM). Critical damage owing to thermal or shock stimuli could translate to significant loss of life and material. The present study models detonation and deflagration of a commonly used granular explosive: cyclotetramethylene-tetranitramine, HMX. A robust literature review is followed by computational modeling of gas gun and DDT tube test data using the Sandia National Lab three-dimensional multi-material Eulerian hydrocode CTH. This dissertation proposes new computational practices and models that aid in predicting shock stimulus IM response. CTH was first used to model experimental data sets of DDT tubes from both Naval Surface Weapons Center and Los Alamos National Laboratory which were initiated by pyrogenic material and a piston, respectively. Analytical verification was performed, where possible, for detonation via empirical based equations at the Chapman Jouguet state with errors below 2.1%, and deflagration via pressure dependent burn rate equations. CTH simulations include inert, history variable reactive burn and Arrhenius models. The results are in excellent agreement with published HMX detonation velocities. Novel additions include accurate simulation of the pyrogenic material BKNO3 and the inclusion of porosity in energetic materials. The treatment of compaction is especially important in modeling precursory hotspots, caused by hydrodynamic collapse of void regions or grain interactions, prior to DDT of granular explosives. The CTH compaction model of HMX was verified within 11% error via a five pronged validation approach using gas gun data and employed use of a newly generated set of P-α parameters for granular HMX in a Mie-Gruneisen Equation of State. Next, the additions of compaction were extended to a volumetric surface burning model of HMX and compare well to a set of empirical burn rates. Lastly, the compendium of detonation and deflagration models was applied to the aforementioned DDT tubes and demonstrate working functionalities of all models, albeit at the expense of significant computational resources. A robust hydrocode methodology is proposed to make use of the deflagration, compaction and detonation models as a means to predict IM response to shock stimulus of granular explosive materials.
ContributorsMahon, Kelly Susan (Author) / Lee, Taewoo (Thesis advisor) / Herrmann, Marcus (Committee member) / Chen, Kangping (Committee member) / Jiao, Yang (Committee member) / Huang, Huei-Ping (Committee member) / Arizona State University (Publisher)
Created2015
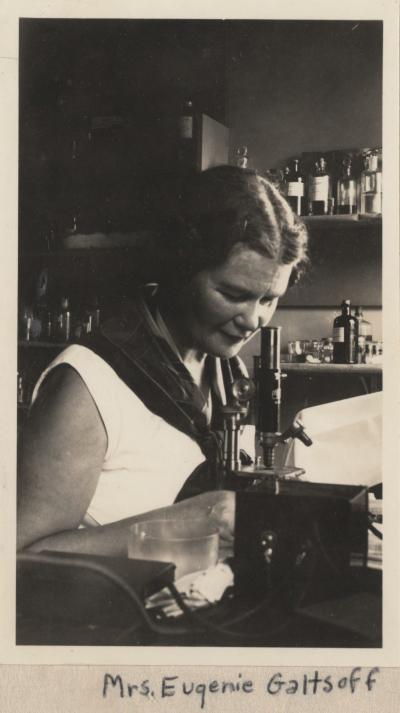
ContributorsMarine Biological Laboratory Archives (Publisher) / Arizona Board of Regents (Publisher)
Created1925-19-39 (uncertain)
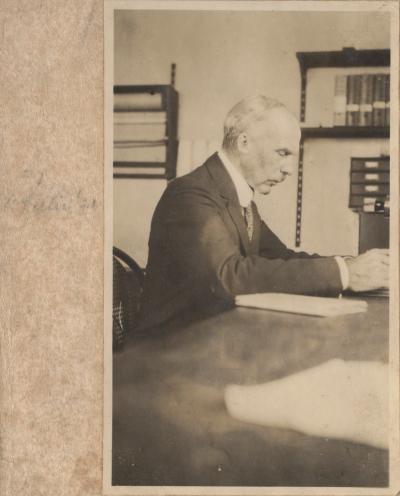
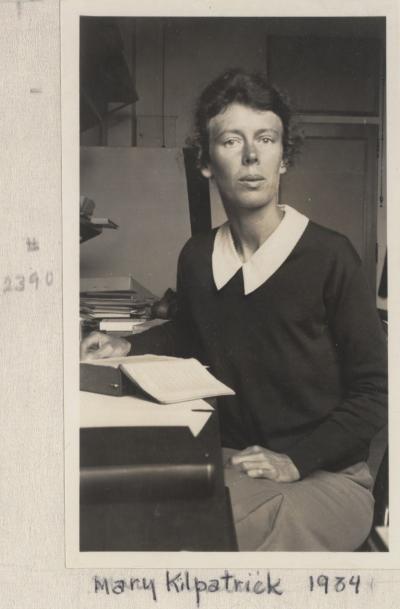
ContributorsMarine Biological Laboratory Archives (Publisher) / Arizona Board of Regents (Publisher)
Created1934
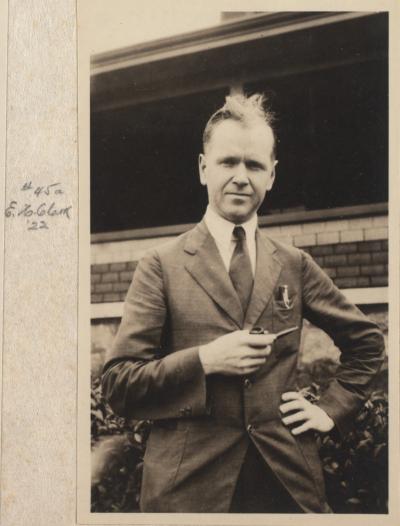
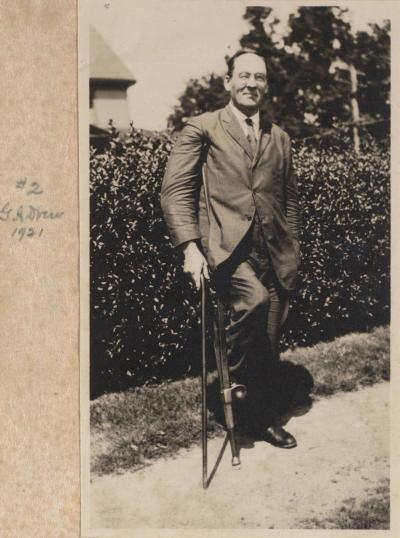
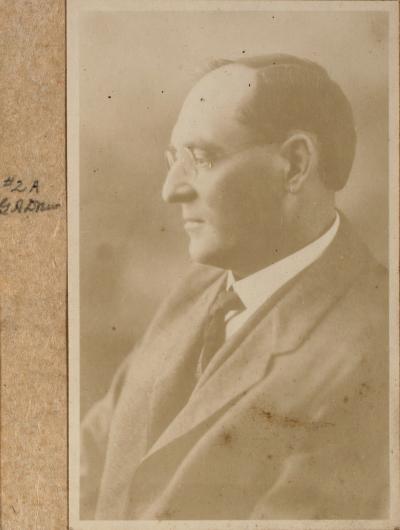
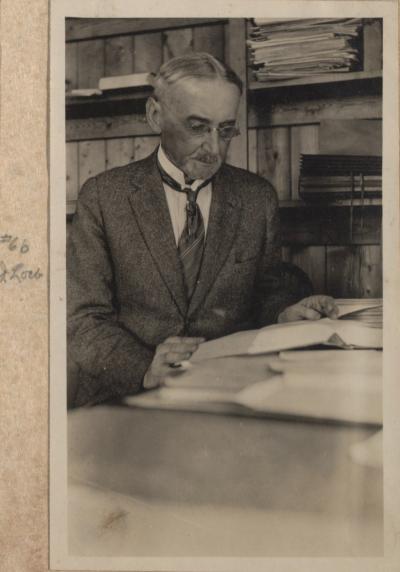